Describe The Creation Of A Sheet Metal Flange
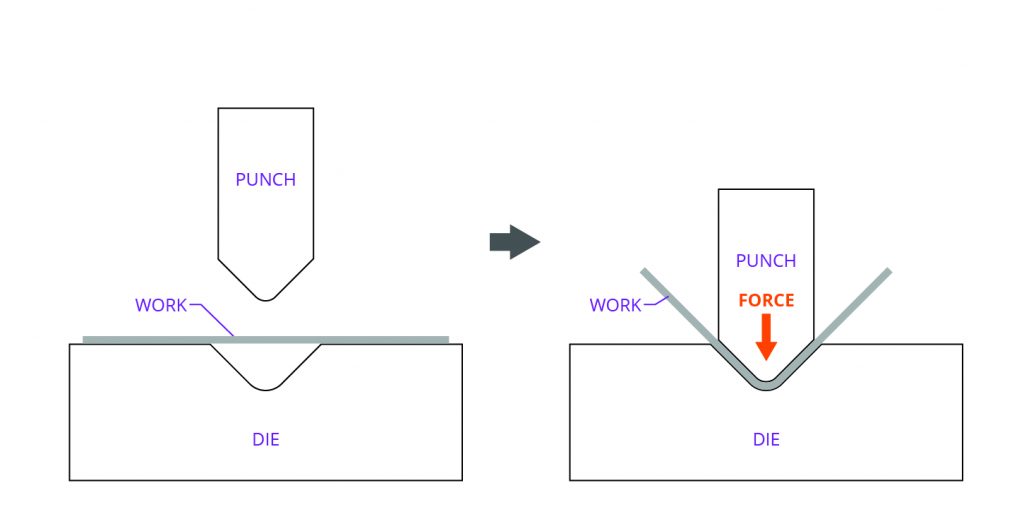
Create a flange in sheet metal and specify the width of the flange.
Describe the creation of a sheet metal flange. In days gone by when most bodywork was done by skilled tinsmiths with no modern machinery many methods of working existed which have largely been forgotten now this is possibly one of them. You can also specify the width or offset of the new flange. Create sheet metal flange with offset width create a flange and define its width as an offset. Create flange with from to selections in sheet metal create a flange and define its width with from to selections.
As per sheet metal design thumb rules the depth of bend relief should be greater than or equal to the inside bend radius of the bend and the width of the bend relief should be the same as the sheet metal thickness or more. During the creation of a sheet metal face the face can extend to meet another face and connect it with a bend. List and describe two of the factors that can change the k factor value. In low carbon steel sheet metal the minimum radius of a bend should be one half the material thickness or 0 80 mm.
The base flange feature is created from a sketch. Notching as discussed is generally a progressive process in the creation of a profile. Design for manufacturability sheet metal guidelines bends for the ease of manufacturing multiple bends on the same plane should occur in the same direction. Use the flange tool on the sheet metal features toolbar to add a sheet metal face and a bend to an existing sheet metal face.
A sheet metal cut that used the distance extents option must be created equal to the thickness parameter. Forming a sheet metal flange. How is the k factor used to calculate the flattened length in sheet metal flat patterns. Flange dialog box defines a flange by adding a sheet metal face and a bend to an edge or edge loop on a face.
Avoid large sheet metal parts with small bent flanges. False true or false. List and describe two of the settings available in the sheet metal defaults in creo parametric. A base flange is the first feature in a new sheet metal part.
Sheet metal manufacturing is a good example of an industry that uses a large amount of progressive processing. Create 3 bend corner on flange in sheet metal while creating a flange add a 3 bend corner using auto miter. In the end of this rod a slot is cut the depth of which is the same as the depth of the flange you wish to create. The only tool you need is a length of 1 2 steel rod about 6 or so long.
A flange feature consists of a face and bend connected to an existing face along a straight edge. When you add a base flange feature to a solidworks part the part is marked as a sheet metal part. The flange which does not have relief will result in a greater amount of distortion or tearing of the adjacent material. Often the order in which the operations occur is important.
Bends are added wherever appropriate and sheet metal specific features are added to the featuremanager design tree. Many other sheet metal cutting operations may occur in a larger progressive process.